防錆・防食溶射 Anti-rust & anti-corrosion thermal spraying
- 鋼材防食技術概要と現状
- 溶射技術の応用分野
- 金属溶射の分類と常温金属溶射の位置付
- 常温金属溶射とは? (Zn/Al擬合金溶射とは?)
- 亜鉛/アルミニウム擬合金溶射皮膜
- 常温金属溶射の防食効果
- 常温金属溶射の作業工程
- 常温金属溶射用標準機器
- 常温金属溶射用標準材料
- 常温金属溶射適用範囲
- 常温金属溶射技術特性
- 常温金属溶射・施工実績例
- パズル®工法 (カタログPDF)
※PDFファイルをご覧いただくためにはAcrobat Readerが必要です。
鋼材防食技術概要と現状
1. 塗料系
塗装は、鋼材表面に形成した塗膜が酸素や水、塩化物イオン等の腐食を促進する物質を遮断することで鋼材を保護する、長い歴史と実績を有する防錆・防食方法である。また、適切な塗替えを行うことにより、防食機能および美観を維持あるいは向上させることができる。
2. 耐候性鋼材
耐候性鋼板は大気腐食に伴って保護性の錆層(安定錆)が形成され、それ以上の腐食を抑制するものであり、適度な環境下では腐食速度がステンレス鋼なみの低さになる。但し、使用環境については、飛来塩分量が0.05mdd(mg NaCl/dm2/day)以下である地域での適用が推奨され、四方を海に囲まれた本国では、米国等に比較して、その適用率が大幅に下回っている。
又、1991年にスパイクタイヤが禁止されて以降、高速道路を中心に凍結防止剤の散布量が増加しており、山間部の橋梁においても保護性錆層の形成が阻害される等の報告もされている。現在、このような課題を解決する意味で、各メーカーにて高塩化物環境下でも無塗装使用が可能なニッケル系高耐候性鋼材等の開発も行われており、適用実例による耐食性向上効果の確認についての確認が待たれている。
3. 溶融亜鉛めっき系
溶融亜鉛めっき系は施工単価が安く、又、防食性能も優れている点より、古くから多方面に広く採用され、信頼性の高い防食工法の一つに挙げられる。しかし、めっき層の制約からくる対応可能な鋼材サイズの制限や、薄板鋼鈑での熱歪、廃液処理規制、現場施工が不可能である等々の問題がある場合は他の防食方法との併用となる。
4. 一般溶射
ガスフレーム亜鉛溶射やアーク亜鉛溶射は、溶融亜鉛めっきと同等の防錆力を有し、以前より重防食施工用として多方面に採用されてきた防食工法の一つである。しかし、高圧ガスを使用する為に、その取り扱いが難しい事(=フレーム亜鉛溶射)、現場対応型が少なく、溶射装置自体の取り扱いが複雑な事(=アーク亜鉛溶射)等、現場ではなく工場施工を活動の中心としている。また、溶射用粗面化処理として、高度なブラスト処理が必須なことなど、作業者の熟練度によるところが多いことも、現場施工に多く普及するに至っていない要因のひとつである。
5. 亜鉛/アルミニウム擬合金常温溶射
防食効果の高い金属(亜鉛/アルミニウム)をアーク熱により溶融し、常温(40℃~70℃程度)で皮膜形成することが可能な金属溶射方法である。
従来から存在する溶射方法(アーク溶射)を改良し開発されたもので、主な特徴として、粗面化処理工程簡素化のため、粗面形成材を使用する点や溶射基材に対して、低温皮膜形成できる点の他に、溶射金属として亜鉛、アルミニウムの2種類を同時に溶かし、複合皮膜化(擬合金)し防錆・防食効果の向上をはかった点等が挙げられる。
また、溶射機も小型軽量化、操作性の簡素化等の改良が加えられ、その結果として、防錆効果の向上だけではなく、作業性が良好となり、基材と溶射皮膜の優れた密着性を発揮する技術に改良されている。
溶射技術の応用分野
『溶射』は、コーティング材料を、加熱により溶融ないしは軟化させ(溶)、微粒子状にして加速し被覆対象物表面に衝突させて(射)、扁平に潰された粒子を凝固・堆積させる事により皮膜を形成するコーティング技術の一種である。
溶射の主なる適用目的・使用材料・適用例を分類すると、下図のようになる。
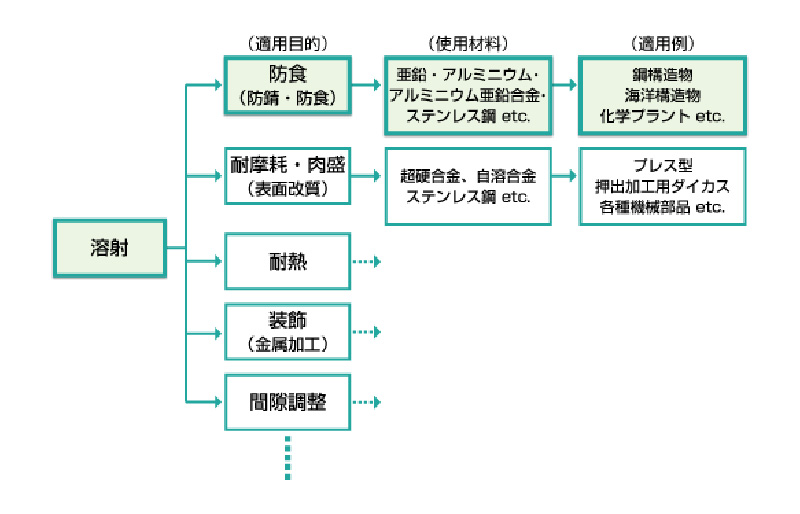
金属溶射の分類と常温金属溶射の位置付
主要な溶射法を熱源の種類により分類すると下図のようになる。
常温金属溶射法は、溶射皮膜形成時の温度が低いことから、溶射皮膜を素地に密着させるアンカーパターンの形成に導電性金属骨材を含有した二液硬化型エポキシ樹脂系粗面形成材の使用を可能にした。(※フレーム溶射など、溶射皮膜形成時の温度が高い溶射法では、粗面形成材が熱で変質劣化し、安定した付着力が得られなかった。)
この技術により、従来はブラスト法によるしかなかった粗面化処理が粗面形成材を適用する事で、粗面化処理前の前処理方法を種々現場条件に合わせて選択(動力工具処理等)できるようになった。
常温金属溶射法は、鋼橋等の防食技術として必要な現場施工が可能な技術といえる。
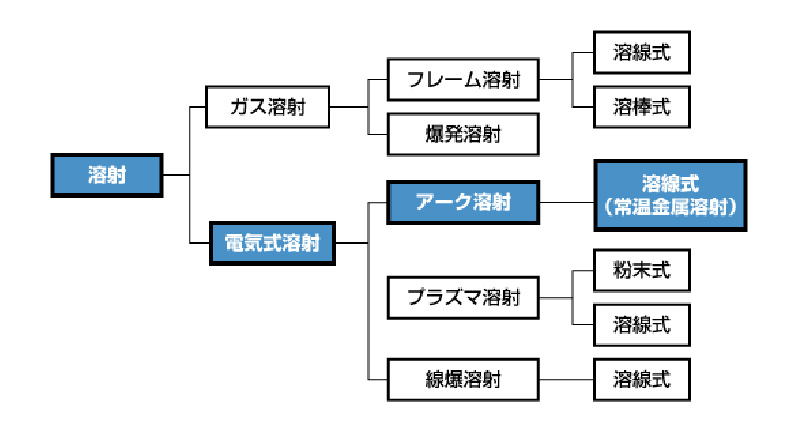